The Innovation and Progress in Polyethylene
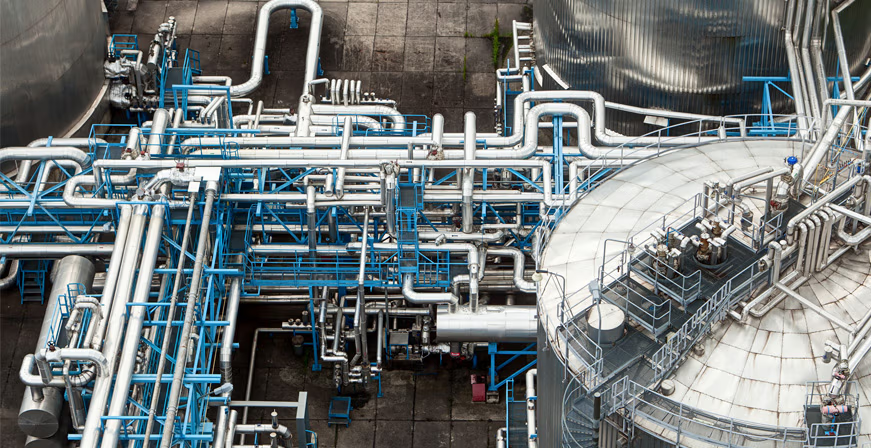
Polyethylene Pipe in the Oil and Gas Industry
From longer lasting to increased flexibility, increased efficiency and innovative installation; high density polyethylene pipes are rapidly becoming the industry standard for oil and gas gathering. Beyond those advantages, the most impactful is that it meets all the standards required to transport natural and other gases, per federal regulations in compliance with 49 CFR 192.
While these pipes are of superior quality and performance, they also represent a significant innovation within the industry that should not be understated. Here’s what you should know.
What is high density polyethylene
High density polyethylene (HDPE) is the classification of the thermoplastic polymer produced from the monomer ethylene. It is naturally lightweight and flexible with a high strength-to-density ratio. Industrial PE4710 is a class of polyethylene commonly used to transport oil and natural gases that meet exceptionally high-performance requirements and is available in Iron Pipe Sizes (IPS) ranging from ¾” to 54 inches, as standardized per ASTM D3035 and ASTM F714.
The benefits of HDPE
HDPE pipes last longer in the ground as the material is resistant to chemicals and damage caused by acids, salts and other. Unlike carbon steel pipes, HDPE pipes do not require special coating to protect against corrosion. Pipes that last longer in the ground contribute to stable pipelines and lower maintenance and replacement costs.
When the terrain of the world doesn’t want to accommodate your pipeline, the flexibility of HDPE really shines. While the polymer is naturally flexible and can flex in and out of trenches, the extent to which the pipe can safely bend in the field depends on the presence of fittings, wall thickness and the diameter of the pipe.
HDPE pipes also support a high flow rate for the material being transported. The smooth interior surface reduces drag, turbulent flow and keeps the coefficient of friction low. Low friction makes the system more efficient and can reduce your pumping costs.
The lightweight structure of HDPE reduces the overall weight simplifying material handling and reducing the price of transportation. This makes it a cost-effective alternative to carbon steel and composite pipe.
Amongst all those benefits, one of the most beneficial features of HDPE pipes is how the industry has innovated around its installation and “welding.” HDPE can be joined pipe-to-pipe, with butt fusion and with proprietary couplings using electrofusion. Both methods result in joints as strong as the original material, are “welded” in the field without an open flame and create a leak-free joint reducing contaminants.
How to connect HDPE pipes
An HDPE pipe must be prepped to be free of contaminants and clean for the heating process. This involves cleaning and may include scraping down to the virgin pipe. If the pipes are straight, they can be joined via butt fusion by heating both ends to a melting point and mechanically pressing them together until cool. A bead will form on both the inside and outside of the pipe, indicating a seal.
When pipes need to change directions and cannot maintain the minimum bending radius, installation typically involves a coupling. From there, couplings are installed using electrofusion — a process where the manufacturer embeds electric heating elements within the coupling to melt the polyethylene from the inside without the need for an open flame.
The electrofusion process showcases a technological advancement that is surprisingly simple for the operator is inserted into the coupling at the required depth. To “shoot the coupling,” the controller’s leads are attached to the coupling and the operator scans the barcode. All the specs for that coupling are loaded on a controller, like a Perc Phoenix Controller, which is verified by the operator before they hit start.
“Cook time” can take anywhere from 24 seconds to 800 seconds, depending on the size of the pipe and ambient conditions. The coupling must sit and cool for a mandatory period before removing the leads and performing a pressure test .
With a passed pressure test, the operator logs their paperwork, and the joining is complete. The barcodes for each coupling enable the operator to log GPS coordinates for each joined joint for future reference or maintenance.
Safety and training
The certification process for electrofusion is required and provided by the manufacturers before you can use and install their product. In addition to annual certifications for the operators, manufacturers and distributors recommend annual calibrations for the controllers (e.g., Perc Phoenix Controller) and power supply.
This dedication to learning is needed to support the continued development of emerging technology and to keep all teams up to date on the safest operations for both personnel and the stability of the pipe.
Nick Torkildsen of Mulcare Pipeline Solutions, Inc. likes to say, “Treat your controller like a computer, not a hammer. Keep it clean from dirt and water and inspect it regularly.”
While the average person doesn’t think about the pipes that deliver natural gas to our community every day, the men and women who ensure their safe installation, maintenance, and monitoring of those pipes understand their responsibility. Innovation and technology like HDPE and electrofusion couplings are driving forward progress within the energy sector that has wide sweeping benefits across multiple industries.
About Catco
Catco helps companies in the oil and gas industry build energy resilience by ensuring their natural gas production, processing, transportation, and distribution continue in any condition. Learn how our products can support your business by scheduling your discovery call today.