Part 1: Gas Conditioning and the Importance of Pressure Control Explained.
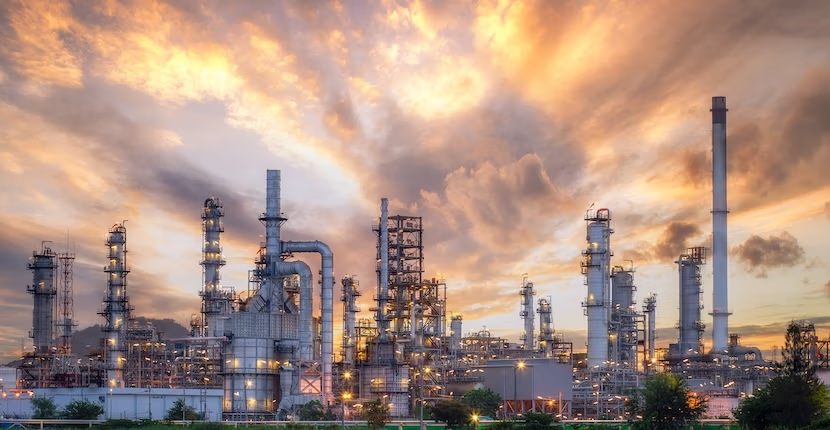
This article is part one of a two-part series. To see part two click here.
In the natural gas industry, maintaining the integrity and efficiency of gas systems is of utmost importance to avoid unnecessary downtime and ensure a reliable supply. One critical aspect is gas conditioning, which involves the removal of impurities to make the gas suitable for various applications.
However, it’s not just about removing impurities; managing gas pressure throughout the conditioning process is equally crucial.
What is an “impurity”?
Impurities in natural gas are substances that are present within the gas stream, including liquid droplets, acid gases, heavy hydrocarbons, and particulate matter. They can enter the natural gas during the production process due to factors like contamination, incomplete purification, or chemical reactions.
The presence of impurities in natural gas can have significant impacts on the overall operation and utilization of the gas:
-
- Liquid droplets can cause pipeline blockages and hinder the smooth flow of gas.
- Acid gases, such as hydrogen sulfide and carbon dioxide, are corrosive to pipelines and equipment and pose risks to the environment and human health.
- Heavy hydrocarbons can increase the viscosity of the gas, making it more difficult to transport through pipelines.
- Particulate matter, including dust and solid particles, can cause mechanical damage to equipment and reduce the efficiency of gas processing and utilization systems.
To ensure the quality, safety, and efficient use of natural gas, removing these impurities through gas conditioning processes is crucial.
What is gas conditioning?
Gas conditioning involves a series of treatments like dehydration, sweetening, and fractionation to eliminate impurities and make the gas suitable for its intended applications. These processes help prevent pipeline blockages, equipment corrosion, reduced flow rates, increased energy consumption, and potential system failures, ensuring a reliable and optimized natural gas supply for various industries and consumers.
-
- Dehydration involves removing moisture from the gas stream to prevent the formation of hydrates, which can cause pipeline blockages.
- Sweetening involves removing acid gases that can corrode pipelines and equipment and harm the environment.
- Fractionation involves separating the heavier hydrocarbons from the natural gas to meet specific product specifications.
During the gas conditioning process, removing at least 99.5% of the particles and impurities present in the natural gas stream is necessary for many critical reasons.
-
- Safety and Compliance: Impurities in natural gas can pose safety risks and regulatory compliance issues. For example, acid gases like hydrogen sulfide can be toxic and corrosive, posing health hazards to workers and causing damage to equipment and infrastructure. Removing a significant portion of these impurities makes the gas safer to handle, transport and utilize in various applications.
- Efficiency and Performance: Impurities in natural gas can have detrimental effects on the efficiency and performance of gas processing and utilization systems. Liquid droplets and particulate matter can cause blockages in pipelines, reducing the flow rates, and hindering the system’s overall performance. By removing a substantial portion of these particles, the gas can flow smoothly, maximizing its utilization efficiency and ensuring optimal system performance.
- Product Quality: Impurities can affect the quality and specifications of natural gas required for specific applications. For instance, heavy hydrocarbons can impact the energy content and combustion characteristics of the gas, affecting its performance in gas turbines or other combustion processes. By achieving a high removal rate of impurities, the resulting gas meets the desired quality standards, ensuring consistent and reliable performance in various industrial and commercial applications.
- Environmental Considerations: Some impurities in natural gas, such as sulfur compounds, contribute to air pollution and environmental degradation when released into the atmosphere. By removing a significant portion of these impurities, the gas conditioning process helps reduce emissions and minimize the environmental impact associated with natural gas production, transportation, and utilization.
Why is pressure control important when it comes to gas conditioning?
Pressure control plays a vital role throughout the gas conditioning processes, as excessive pressure can lead to operational issues such as reduced flow rates, increased energy consumption and potential system failure. High pressure can strain pipelines and equipment, increasing the risk of leaks, ruptures or other mechanical failures. By implementing effective pressure control measures, operators can maintain optimal pressure levels, ensuring smooth and efficient gas conditioning operations while mitigating the risk of damage to infrastructure and equipment.
Pressure control is equally critical in pipelines that transport natural gas over long distances, as it experiences frictional losses and pressure drops. To maintain the desired flow rates and ensure efficient transportation, pressure control devices, such as regulators and control valves, are strategically placed along the pipeline network.
Proper pressure control in pipelines not only facilitates the smooth flow of gas but also minimizes the risk of system instability, including issues like cavitation or excessive pressure differentials. Additionally, maintaining consistent pressure levels in pipelines enhances system integrity, reduces the likelihood of leaks or bursts, and promotes safe and reliable gas transportation to end users.
As gas conditioning plays a vital role in ensuring the quality, safety and efficiency of natural gas, it’s essential to maintain effective pressure control to prevent operational issues and maintain optimal flow rates.
This article is part one of a two-part series. To see part two click here.